Non-Pressurized pipe systems are usually Mains, Horizontal Laterals, Vertical Stacks, Sanitary Systems, Storm/Roof Drains, Vent Systems, Processed/Industrial/Chemical Piping, and Other Waste Systems.


Non-Pressurised pipe systems
History of the product
In the early 1970’ s, Eric Wood developed the first cured-in-place pipe technology (CIPP) in England. He then named the CIPP process Insitu form, meaning “form in place” in Latin. Wood received patent no. 4009063 for this technology on February 22, 1977, and was commercialised by Insituform Technologies on February 22, 1994, when CIPP entered the public domain.
During this time the CIPP market’s main focus was on large diameter pipes from 4” to 118” and geared towards the municipal sector. This process was called “inversion” and required large equipment and in most cases, would require digging pits for it to effectively work.
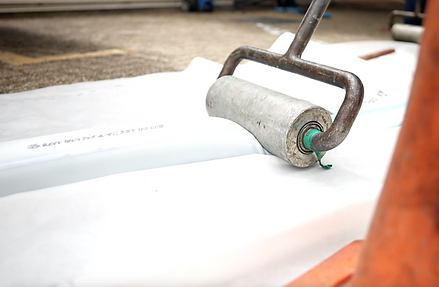
GRPR pull-in-place method has revolutionised the CIPP market by bringing the structural liner inside the building. The pull-in-place method requires the use of existing access points along with the flexibility in the product and how to apply it. The process allows for full control by pulling or pushing the liner into place, a perfect match for large projects within the building’s infrastructure.
What is Pull-in-Place pipe lining?
Pull in place pipe lining is an effective process that restores corroded or eroded drain, waste and vent piping systems without the costly expense and destruction required to replace pipes.
Pipe lining provides an efficient and effective alternative.
-
Significant savings over repipe or pipe replacement
-
Increases life of piping
-
Very little disruption, if any
-
Preservation of building structure and surrounding landscape or hardscape
-
Little to no destruction to the property


Common failures with non-pressurised pipes
-
Clogged or backed up
-
Loss of structure and pipe is caving
-
Tree root intrusion of the pipe
Pipe replacement in aging facilities, the traditional alternative to pipe lining, comes with a host of concerns and issues that must be dealt with, some of which can render such work highly prohibitive. These include:
-
Destruction of existing walls, ceilings, floors and underground structures
-
Patching and repair of the damaged structure
-
Inconvenience and disruption to building/facility occupants or residents
-
Safety concerns where asbestos insulation or other contaminants are present
-
The need to temporarily vacate occupants and dwelling tenants
-
High monetary cost